Top 3 Logistics Management Trends Taking Center Stage in 2019
There have always been three major pillars in the market.
Need |
Product |
Logistics |
The demand and supply form the basis of it all, but there’s this common area between both, logistics management. For the supply, the logistics part seems obvious. But it’s also the inherent part of demand. Demand and supply move in a circular manner just because of the logistics involved. Only when the delivery promises are met, does the demand becomes sustainable, accountable, and predictable.
A few things that are and will shape how logistics is handled, and (by extension) business is conducted are:
1. Demand analysis, predicting business feasibility and profitability
We have new standards in these set by the likes of Amazon, Alibaba, Walmart, Flipkart, and others. To engage customers in the market, to keep them coming back, you need to keep your logistics should be top-notch: agile and fast. For this, you need to be ever alert with instant notifications for whatever’s happening on-ground. Live logistics planning is a necessity. That’s why you keep hearing about end-to-end logistics movement visibility, we’ll come back to this as the direct benefit comes in compliance.
Recommended Read: This Is How You Make Your Logistics Management Truly “Live”!
At the demand analysis and prediction level, live supply chain visibility software helps you understand how your customers are interacting with your last mile leg so that you can react faster and fix better. Suppose, you know the last delivery to a loyal customer wasn’t up to the mark. You can immediately put in a process where such customers are engaged with proper service or offers.
Knowledge is power. Knowledge of live on-ground activities and their consequences is a great business asset.
With this, you can plan to sustain demand over months, giving your forecast much more credibility and help you plan your future logistics investments better without being stuck with random fluctuations and losses dues to idle or over capacity within your fleet. On that note…
2. Capacity optimization for your fleet and drivers
With the growing demand in retail and e-commerce, capacity and resource constraints are rising in logistics and transportation. This includes vehicle’s carrying capacity and skilled driver availability.
Vehicle or fleet carrying capacity can be planned using a composite planning engine which takes into account everything from customer preferred delivery times, optimized route plan covering more parcel deliveries, avoiding unnecessary delay/detention due to traffic or other reasons, and more.
In a more direct manner, a vehicle’s capacity can be optimized using the delivery schedule in a streamlined manner, with in-app scanning of parcels, faster sorting, loading, and dispatch. This comes, again, from a faster system which plans your logistics live and quickly.
LogiNext’s system can plan routes for thousands of parcels in minutes so your vehicles don’t have to wait to be loaded.
Recommended Read: Why Advanced Delivery Route Planning Is Great For The Global Economy?
You’d know which drivers are best-suited with this system. Their skill-sets are predefined and analyzed by the software. If they know a locality better than others, they would be moving smoother there; if they have more experience carrying one type of load (for example, heavy goods or cold-storage units) or handling one type of truck (perhaps box type or reefer); the system can factor these in and auto-allocate, consider every other aspect, the right load to the right vehicle and the right driver at the right time.
3. On-the-road: Knowing where the shipment is, at all times
Now the shipment is out fast, everything went according to plan, yet you are skeptical. With experience, you know that the best-laid plans never see exact execution. There’re always unexpected things that happen on-ground in logistics. That’s why live tracking of each truck is of utmost importance. Live logistics planning and tracking within a single screen would give you a complete outlook of what is being shipped, where it is, and how it is being handled at that time. It just makes your reaction time almost instantaneous.
You know that the trucks, perhaps from external carriers, are transporting your branded products. Being alert is the best protection against any risk that might come by. Using machine learning enabled delivery route planning you have already set your trucks out on the best routes, but there’s still a lot to be done. Companies like LogiNext, extend the route planning to the dynamic limit. You can reroute your trucks whenever required easily, without affecting any ETAs.
All ETAs, even though they were previously accurately predicted, are recalibrated taking in live traffic and other data.
It just gives you more control over on-ground communication and customer expectations. Your customer would know exactly when their parcel would arrive, even track it live on their smartphones. Instant alerts about any ETA updates would be sent directly to them. Wouldn’t a customer who knows that there is a 30-min delay more composed than one who has no idea where their parcel is and when it would reach them? Such compliances are the mainstay of the technology advances that have pushed logistics into the forefront to become a top-line pushing pillar for companies.
Recommended Read: Cloud-Based Machine Learning In An Omnichannel World: Decoding Customer Satisfaction
The main takeaway here is that technology would be the main driver for logistics streamlining all processes so that the focal point is always customer satisfaction.
247 4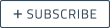
Pingback: Top 3 trend-points and predictions for CPG companies in 2019 - 24/7 Customs Broker News
Pingback: LogiNext-Blog | Top 3 trend-points and predictions for CPG companies in 2019
Pingback: LogiNext-Blog | Case Study: Customer-Centric Live Logistics Optimization for Large Online Retailer
Pingback: LogiNext-Blog | How Cloud-Based Tech Is Changing The Fleet Management Landscape