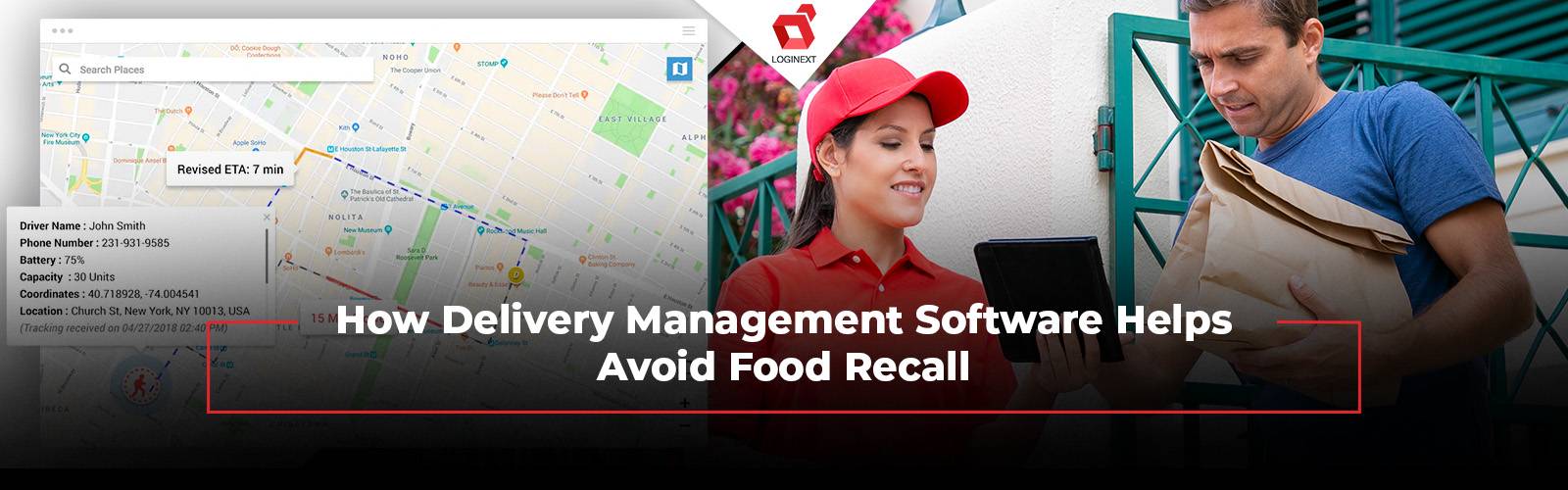
How Does Delivery Management Software Help Avoid Food Recall?
Did you know that in the United States alone, there are thousands of food recalls every year? For example, in 2023, over 300 food recalls were issued due to contamination and labeling issues. These recalls affect not only the health of consumers but also the reputation and finances of food businesses. Delivery Management Software (DMS) can help prevent these costly and dangerous food recalls.
DMS is a powerful tool that allows food companies to track deliveries in real-time. It helps monitor the conditions under which food is transported, and ensure that all safety standards are met throughout the delivery process. By using delivery management software, companies can quickly identify and address potential issues before they become serious problems, reducing the risk of food recalls. This software helps maintain high standards of food safety, ensuring that consumers receive safe and high-quality products.
Check Out: The Top 7 Best Delivery Management Software in the Market
Understanding Food Recalls
A food recall happens when a company removes a food product from the market. This usually happens because the food is not safe to eat. The company or government finds out that the food could make people sick. They then tell stores and consumers to stop selling or eating the food.
Common Causes For Food Recall
Contamination: This occurs when harmful bacteria, viruses, or chemicals get into the food. For example, food can be contaminated with Salmonella or E. coli.
Mislabeling: Sometimes, the labels on food packages are wrong. For example, a product might not list all the ingredients, such as nuts or dairy, which can be dangerous for people with allergies.
Allergens: If food contains allergens like peanuts, eggs, or soy but does not mention them on the label, it can cause serious allergic reactions.
Foreign Objects: Occasionally, things like metal, glass, or plastic end up in food by accident during the production process.
Food Recall Impact on Businesses
Food recalls can have serious impacts on businesses:
Financial Costs: Recalls are expensive. Companies lose money because they have to take products off the shelves and sometimes destroy them. They might also face fines and lawsuits.
Consumer Trust: When a recall happens, people may lose trust in the company. They might stop buying the company’s products, which can hurt sales.
Operational Disruption: Recalls can disrupt normal business operations. Companies need to stop production lines, investigate the problem, and fix it. This takes time and resources.
Delivery Management Software can help businesses avoid these problems. By using DMS, companies can track their deliveries, ensure food is transported safely, and quickly identify issues before they lead to a recall.
The Role of Delivery Management Software to Avoid Food Recall
Delivery Management Software is a tool that helps businesses manage their deliveries. It ensures that products get from the warehouse to the customer safely and efficiently. DMS does this by tracking deliveries, planning the best routes, and keeping records of each delivery.
Delivery Management Software is essential for keeping food safe during transport. It helps companies track deliveries, plan the best routes, and keep accurate records. With DMS, businesses can prevent problems that could lead to food recalls and ensure their customers get safe, high-quality food.
Must Read: Your One-Stop Guide to Delivery Management Software Solution
Prevention of Food Recall through Traceability in Delivery Management Software
Enhanced Traceability
Traceability means being able to track every step of a product’s journey from the supplier to the consumer. Delivery Management Software makes this easier. It helps companies see where their food products are at any time. With DMS, businesses can track food from the moment it leaves the supplier until it reaches the consumer. This way, if there is a problem, they can quickly find out where it started and fix it.
Batch Tracking
Batch tracking is a key feature of DMS. It involves keeping track of groups of products, known as batches. Each batch gets a unique code. This code helps companies know exactly where and when the batch was produced, packed, and delivered.
Importance of Batch Tracking:
Quick Identification: If there is a problem with a batch, like contamination, companies can quickly find out which batch it is.
Isolating the Issue: Once they know which batch has a problem, they can isolate it. This means they can stop selling and recall only the affected batch, not all products.
Preventing Wider Issues: By isolating the problematic batch, companies prevent the issue from spreading and affecting more products.
Explore: Streamline Delivery Operations With Delivery Tracking Software
Let’s Look At A Real-World Example Of How Delivery Management Software Helped Avoid A Food Recall Through Effective Traceability
A dairy company uses DMS to track its milk products. One day, they find out that some milk cartons might be contaminated. Thanks to batch tracking in their DMS, they quickly identify the exact batch that might be affected. They trace the batch back to a specific time and place of production.
With this information, the company immediately stops shipping milk from that batch. They also contact stores to remove the specific batch from shelves. Because they acted quickly, only a small number of cartons were affected. The rest of their products remained safe for consumers.
By using Delivery Management Software, the dairy company prevented a bigger problem. They avoided a large-scale recall and ensured that most of their products stayed safe and available for their customers.
Improved Communication and Coordination via Delivery Management Software
Centralized Communication
Delivery Management Software helps everyone involved in the delivery process stay connected. This includes suppliers, drivers, and retailers. DMS creates a central hub where all information is shared. This means everyone can see the same information and work together more effectively.
Discover: Communication Strategies For Seamless Order Lifecycle Management
Benefits of Centralized Communication:
Smooth Coordination: Everyone knows what is happening at each step of the delivery process. This helps avoid confusion and mistakes.
Faster Responses: If a problem arises, everyone is informed immediately. They can quickly work together to solve it.
Instant Alerts
One of the most powerful features of DMS is instant alerts. These are automatic messages that let people know about potential problems right away.
How Instant Alerts Help?
Early Warning: If something goes wrong, like a temperature spike in a delivery truck, the system sends an alert. This early warning helps prevent spoiled or contaminated food from reaching consumers.
Quick Action: With instant alerts, issues can be fixed immediately. For example, if a truck breaks down, an alert is sent. The company can then send another truck to pick up the food and ensure it is delivered on time.
Find Out: Power Of Alerts And Notifications in Delivery Management
Learn How Frozen Food Companies Avoid Food Recall
A frozen food company uses DMS to manage their deliveries. One day, a truck carrying frozen vegetables breaks down. The DMS sends an instant alert to the manager. The manager sees the alert and immediately contacts another nearby truck to pick up the frozen vegetables.
The vegetables are transferred quickly, and the new truck continues the delivery. Because of the instant alert, the vegetables stay frozen and safe to eat. The company avoids a potential recall by making sure the food is delivered in good condition.
Delivery Management Software improves communication and coordination by creating a central hub for information sharing and providing instant alerts. These features help prevent problems and ensure that food is delivered safely. Real-world examples, like the frozen food company, show how effective communication through DMS can prevent potential food recalls.
Compliance and Documentation using Delivery Management Software
Regulatory Compliance
Food safety regulations are rules that businesses must follow to make sure their food is safe. These rules can be strict and require lots of paperwork. Delivery Management Software helps businesses meet these rules by keeping accurate records and documentation.
How DMS Helps?
Keeps Records: DMS keeps detailed records of every delivery. This includes times, temperatures, and other important details.
Easy Access: If a company needs to show proof of compliance, they can quickly access these records.
Digital Records
Digital records are better than paper-based systems in many ways.
Benefits of Digital Records:
Speed: Digital records are faster to create and update. This saves time compared to writing everything by hand.
Accuracy: Digital records reduce mistakes. They automatically capture information, so there is less chance of errors.
Accessibility: Digital records are easy to find and share. Anyone with permission can access them from anywhere. This is helpful during audits or investigations.
Don’t Miss: What Is EPOD And Why Is It A Must For Your Delivery Business?
How Does Fresh Produce Company Avoid Food Recall Using Delivery Management Software?
A fresh produce company uses DMS to keep digital records of their deliveries. During an audit, inspectors ask to see the company’s delivery records. The company quickly pulls up the digital records on their computer.
The records show detailed information about each delivery, including dates, times, and temperatures. The inspectors are impressed by how organized and accurate the records are. They finish the audit quickly, and the company passes without any problems.
Later, the company faces a recall investigation. They use their DMS to track down all the batches of a specific product. The digital records help them identify which batches might be affected. They quickly inform stores and remove the affected batches from shelves. This quick action prevents a larger recall and keeps customers safe.
Delivery Management Software helps businesses comply with food safety regulations by maintaining accurate digital records. Digital records are faster, more accurate, and easier to access than paper-based systems. Real-world examples, like the fresh produce company, show how digital documentation through DMS can help during audits and recall investigations.
Enhancing Quality Control by Integrating Delivery Management Software
Real-Time Monitoring
Delivery Management Software helps businesses keep an eye on delivery conditions in real-time. This means they can monitor things like temperature and humidity as food is being transported.
How Real-Time Monitoring Works?
Sensors: Special sensors in delivery trucks track conditions such as temperature and humidity.
Instant Updates: The sensors send instant updates to the DMS, showing the current conditions.
Alerts: If the conditions go outside safe ranges, the DMS sends an alert so the problem can be fixed right away.
Why It’s Important?
Food Safety: Keeping food at the right temperature and humidity levels ensures it stays safe to eat.
Prevent Spoilage: Monitoring conditions helps prevent food from spoiling during transport.
Quality Control Checks
DMS also helps with automated quality control checks at different points in the delivery process.
How do Quality Control Checks Work?
Automated Systems: The DMS sets up checkpoints where the quality of the food is checked automatically.
Data Collection: At each checkpoint, the system collects data on things like temperature, packaging integrity, and delivery times.
Alerts for Issues: If there is a problem, such as a temperature spike or damaged packaging, the system sends an alert.
Why It’s Important?
Consistent Quality: Automated checks ensure that the food meets safety standards at every step.
Quick Responses: If an issue is found, it can be fixed right away before the food reaches the consumer.
How Can Seafood Companies Avoid Food Recall Using Delivery Management Software?
A seafood company uses DMS to ensure the safety of their deliveries. Seafood is very sensitive to temperature changes, so they need to keep it cold at all times.
Real-Time Monitoring:
Sensors in Trucks: The trucks have sensors that monitor the temperature inside the storage area.
Immediate Alerts: One day, the temperature in a truck starts to rise because of a malfunctioning cooler. The DMS sends an immediate alert to the manager.
Recommended Read: Revolutionize Your Retail Delivery With Compartment Planning
Quality Control Checks in Delivery Management Software:
Regular Checkpoints: The DMS has set checkpoints where the temperature and packaging are checked automatically.
Action Taken: When the alert about the rising temperature is received, the company quickly sends another truck with a working cooler. The seafood is transferred to the new truck.
Get Insights: Do You Have Multi-Compartment Vehicles? We Got Your Back!
Outcome Using Delivery Management Software:
Food Safety Maintained: Because of real-time monitoring and quick action, the seafood stays at a safe temperature.
Avoided Spoilage: The company avoids having to throw away spoiled seafood and prevents any potential food safety issues.
Delivery Management Software enhances quality control by allowing real-time monitoring of delivery conditions and automated quality control checks. These features help ensure that food stays safe and meets high standards throughout the delivery process. Real-world examples, like the seafood company, show how DMS can prevent food safety issues and maintain product quality.
Learn More: The Vital Role Of Transportation Planning In Modern Business
Finding Ideal Delivery Management Software For Fresh and Fast Delivery
Investing in Delivery Management Software is crucial for any food business. DMS helps prevent food recalls by improving traceability, communication, compliance, and quality control. It ensures that food is transported safely, meets all safety standards, and arrives fresh and uncontaminated. By using DMS, businesses can save money, protect their customers, and maintain their success.
If you are a business owner or manager in the food industry, now is the time to explore Delivery Management Software solutions. DMS can help you manage your deliveries more efficiently and keep your food products safe. Don’t wait until a food recall happens. Make the smart choice today. Invest in Delivery Management Software and ensure the safety and quality of your food products.
64
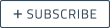
@LogiNext