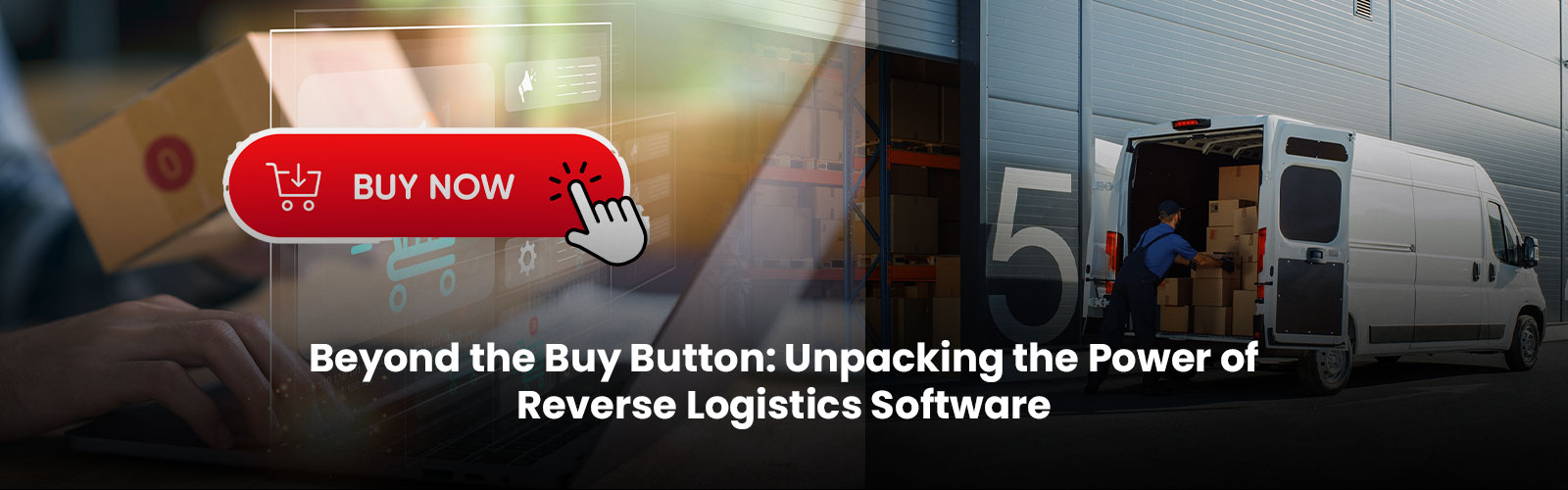
Beyond the Buy Button: Unpacking the Power of Reverse Logistics Software
In today’s fast-paced, customer-centric supply chain environment, reverse logistics is no longer an afterthought. With the surge in eCommerce returns and sustainability efforts, businesses must adopt efficient systems to handle returns, refurbishments, recycling, and more. This is where Reverse Logistics Software steps in — a game-changer for modern logistics operations.
In this comprehensive guide, we explore the benefits, core features, and best practices for leveraging reverse logistics software. Whether you’re a retailer, distributor, or manufacturer, understanding this essential technology is key to improving customer satisfaction, cutting costs, and building a more sustainable supply chain.
What is Reverse Logistics Software?
Reverse logistics software refers to digital platforms that manage and streamline the movement of goods from the customer back to the seller or manufacturer. This can include product returns, repairs, recycling, disposal, or resale. Unlike forward logistics, which focuses on getting products to customers, reverse logistics deals with their journey back.
A robust reverse logistics system enables businesses to reduce operational bottlenecks, automate returns processing, and gain visibility into product lifecycles.
Why Reverse Logistics Matters Today
In an era defined by rapid eCommerce growth, managing returns efficiently is crucial. Global return rates can exceed 30% in sectors like fashion and electronics, leading to significant reverse flow costs and inventory challenges. Without a robust reverse logistics solution, businesses face manual bottlenecks, misrouted items, and lost revenue.
Moreover, consumers now expect seamless, sustainable return processes—brands that fail to deliver risk damaging loyalty and reputation. Implementing a dedicated reverse logistics system not only cuts processing time and operational expenses but also supports environmental initiatives by enabling recycling, refurbishing, and proper disposal. In today’s market, reverse logistics technology is a strategic imperative.
Key Benefits of Reverse Logistics Software
Implementing the best reverse logistics software offers several transformative benefits:
1. Enhanced Customer Experience:
Fast, hassle-free returns lead to increased customer loyalty. Automated return labels, real-time tracking, and easy-to-use portals reduce frustration and build trust.
2. Reduced Operational Costs:
Manual handling of returns is labor-intensive and error-prone. A digital reverse logistics platform automates workflows, cutting labor expenses, minimizing mistakes, and accelerating processing times.
3. Real-Time Visibility and Analytics:
Gain full transparency into return flows. Detailed dashboards track KPIs—return rates, processing time, and recovery value—so teams can spot trends, identify root causes, and optimize processes.
4. Sustainability and Compliance:
Ensure proper documentation for recycling, refurbishing, and disposal. A reverse logistics solution helps meet environmental regulations and supports corporate social responsibility goals.
5. Improved Inventory Recovery:
Quickly assess returned items for resale, refurbishment, or recycling. By maximizing asset recovery, companies reduce write-offs and recapture value from returned goods.
Must-Have Features in Reverse Logistics Software
When selecting a reverse logistics solution, ensure it includes these core features:
1. Automated Return Authorization (RMA):
Simplify the process of returns with automated approvals and notifications based on pre-set business rules. This reduces manual intervention and speeds up customer refunds or exchanges.
2. Multi-Channel Integration:
A good reverse logistics platform should integrate with your eCommerce, ERP, WMS, and TMS systems to enable seamless data exchange and end-to-end visibility. This ensures return data flows smoothly across all your operational tools.
3. Real-Time Tracking:
Give customers and internal teams the ability to track returns in real-time—from pickup to warehouse to processing. This transparency reduces inquiries and builds trust.
4. Condition Grading and Inspection Tools:
Enable warehouse teams to inspect and categorize returned goods effectively, speeding up restocking, refurbishing, or disposal. Detailed grading criteria help maximize asset recovery.
5. Analytics and Reporting Dashboard:
Use dashboards to track KPIs like return rates, cost per return, average processing time, and recovery rates. Actionable insights help refine policies and improve efficiency.
6. Regulatory Compliance Support:
Ensure the platform helps with document generation and compliance reporting, especially for items like electronics or hazardous materials. This mitigates legal risks and supports sustainability goals.
Best Practices to Maximize ROI from Reverse Logistics Technology
Investing in the right reverse logistics technology is only part of the equation. Here’s how to ensure long-term success:
1. Define Clear Return Policies:
Transparency is key. Ensure your return policies are well-communicated, easy to understand, and supported by your software platform.
2. Train Your Teams:
Warehouse staff and customer service agents should be trained to use the software efficiently. Accurate grading and timely processing lead to better results.
3. Leverage Data for Strategic Decisions:
Use software analytics to understand patterns in product returns, identify quality issues, and adapt your procurement or manufacturing strategies accordingly.
4. Optimize Your Reverse Supply Chain:
Evaluate if returns should go back to the original fulfillment center, a central returns facility, or a refurbishing partner. Let the software guide decision-making based on cost and efficiency.
5. Continuously Evaluate Software Performance:
Track the performance of your reverse logistics system against defined KPIs and user feedback. Look for new updates and features that can enhance performance.
How to Choose the Best Reverse Logistics Software
When evaluating vendors, look for these differentiators:
– Scalability: Can it grow with your business and handle peak return seasons?
– Customization: Does it support the specific workflows and products in your business?
– Support & Onboarding: Is training, onboarding, and post-deployment support comprehensive?
– Security: Are data and transaction security standards met?
Popular industries benefiting from reverse logistics software include retail, electronics, automotive, pharmaceuticals, and consumer goods.
Future Trends in Reverse Logistics Technology
As customer expectations and environmental concerns rise, the reverse logistics technology landscape is rapidly evolving. Here are a few trends to watch:
– AI and Machine Learning: Predict return reasons and automate decisions for restocking, recycling, or refurbishing.
– Blockchain: Improve transparency and traceability, especially for high-value goods and warranty claims.
– IoT Integration: Use sensors to monitor product condition and automate inspection processes.
Final Thoughts
Efficient reverse logistics is no longer just a cost center — it’s a competitive advantage. With the right reverse logistics software, businesses can reduce costs, boost customer satisfaction, and contribute to sustainability.
Whether you’re aiming to implement the best reverse logistics software, upgrade your existing reverse logistics platform, or explore a future-ready reverse logistics system, now is the time to act.
A strategic investment in reverse logistics solutions will not only streamline your return flows but also set your brand apart in a crowded market. So, click on the red button below and book a demo with LogiNext Solutions today!
Like
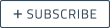
@LogiNext