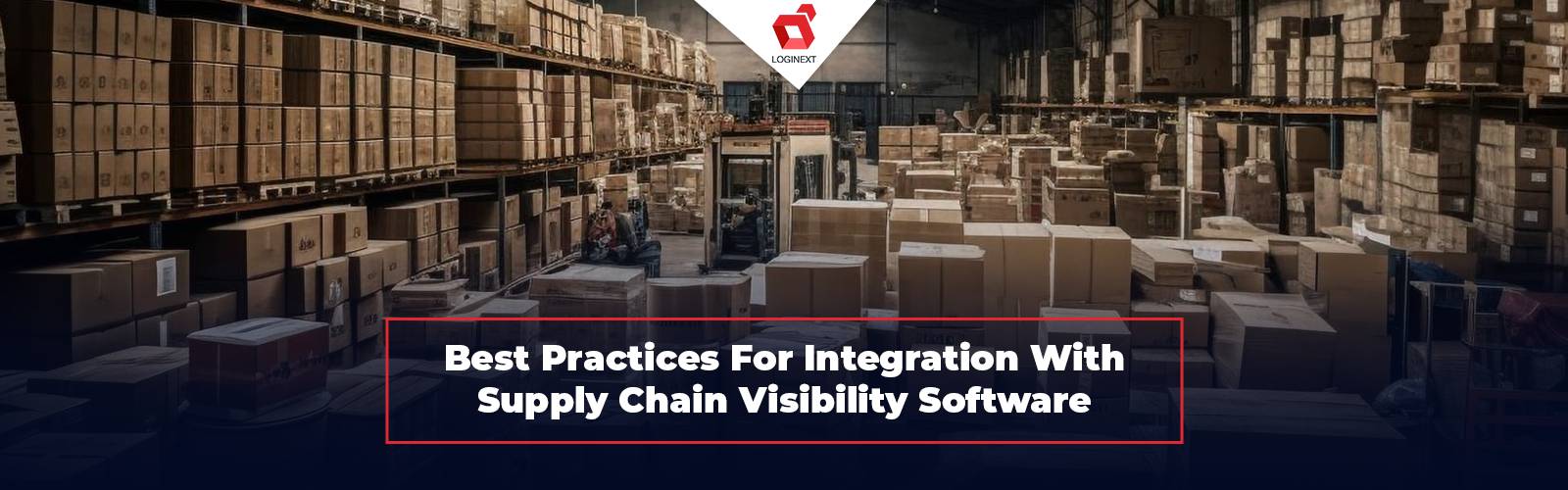
Best Practices for Successful Implementation and Integration of Supply Chain Visibility Software
In today’s fast-paced business environment, supply chain management plays a crucial role in determining the success and competitiveness of companies across various industries. To stay ahead of the competition and meet customer expectations, C-level executives of the supply chain need to embrace innovative technologies. It will enhance visibility, efficiency, and collaboration within their supply networks. This is where supply chain visibility software comes into play.
In this blog post, we will explore the best practices for successfully implementing and integrating a supply chain visibility system into your organization. We will discuss-
– The importance of supply chain visibility
– Key considerations for supply chain visibility software selection
– Implementation strategies for supply chain visibility tool
– Integration challenges in supply chain management
– How to measure the success of your supply chain visibility system?
The Importance of Supply Chain Visibility
Supply chain visibility refers to the ability to track products/ goods, and information as they flow through the supply chain. It enables organizations to gain real-time insights into their supply network, identify bottlenecks, optimize inventory levels, improve customer service, and enhance overall operational efficiency.
A report from GlobeNewswire states that the Global Supply Chain Visibility Software market size was valued at $1.205 billion in 2022 and is expected to reach $4.928 billion in 2028.
With supply chain visibility software, companies can have complete control over their supply chain operations. Software like LogiNext Mile can proactively address disruptions, mitigate risks, reduce lead times, and make informed decisions based on accurate and up-to-date information. This level of visibility not only improves operational efficiency but also strengthens relationships with suppliers, customers, and other stakeholders.
Selecting the Right Supply Chain Visibility Software
Choosing the right supply chain visibility system is a critical decision that can significantly impact the success of your implementation. Here are some key considerations to keep in mind during the selection process:
- 1. Define your objectives and requirements
Before evaluating different software solutions, it is essential to clearly define your objectives and requirements.
What specific challenges are you looking to address with supply chain visibility software?
Do you need end-to-end visibility or focus on specific areas?
By having a clear understanding of your needs, you can narrow down your options and ensure that the selected software aligns with your goals.
- 2. Look for scalability and flexibility
As your business grows and evolves, your supply chain visibility software requirements may change. It is crucial to choose a software solution that can scale your business and adapt to future needs. Look for a flexible platform such as LogiNext Mile, that can integrate with your existing systems and easily accommodate changes in your supply chain processes.
- 3. Evaluate user-friendliness and ease of implementation
Consider the usability and intuitiveness of the software interface.
Will your employees find it easy to use?
Complex and difficult-to-navigate systems may lead to resistance and hinder successful adoption. Also, assess the implementation process.
Does the software provider offer training and support?
A smooth and efficient implementation of a supply chain visibility system is crucial for minimizing disruptions to your operations.
- 4. Assess data security and system reliability
Supply chain visibility involves the sharing of sensitive information across various stakeholders. It is imperative to ensure that the software provider has robust security measures in place to protect your data from unauthorized access or breaches. Additionally, consider the system’s reliability and uptime. Downtime can have severe consequences on your supply chain operations, causing delays and missed opportunities.
Implementing Strategies For Supply Chain Visibility Tool
Once you have selected the right supply chain visibility software, a well-planned implementation strategy is crucial for success. Here are some best practices to consider during the implementation process:
- 1. Set clear implementation goals
Clearly define the goals and objectives of your implementation of a supply chain visibility tool.
What specific outcomes are you looking to achieve?
Communicate these goals to your implementation team and stakeholders to ensure everyone is aligned and working towards the same objectives.
- 2. Establish a dedicated implementation team
Assign a dedicated team to lead the implementation of the project. This team should include representatives from different departments, including supply chain, IT, operations, and finance. Establish clear roles, responsibilities, and timelines for each team member to ensure effective coordination and accountability in implementing the supply chain visibility tool.
- 3. Conduct a thorough data analysis
Before implementing the supply chain visibility software, analyze your existing data and processes. Identify any data gaps, inconsistencies, or redundancies that need to be addressed. Cleanse and standardize your data to ensure its accuracy and reliability in the new system.
- 4. Define key performance indicators (KPIs)
Determine the KPIs that will measure the success of your supply chain visibility system. These KPIs should align with your implementation goals and reflect the desired outcomes.
Examples of relevant KPIs include on-time delivery, inventory turnover, order fulfillment cycle time, and supplier performance. All of this can be easily recorded and analyzed using LogiNext Mile.
- 5. Provide comprehensive training and support
Ensure that your employees receive proper training on how to use the new supply chain visibility tool effectively. This training should go beyond the technical aspects and also cover the strategic benefits and best practices. Additionally, provide ongoing support to address any questions or challenges that arise during the implementation phase.
Integrating Supply Chain Visibility Software For Smoother Supply Chain Management
Integrating a supply chain visibility system with your existing systems and processes is often a complex task. Here are some considerations to ensure a smooth integration:
- 1. Evaluate supply chain software integration capabilities
During the software selection process, assess the integration capabilities of the solution.
Does it have pre-built connectors or APIs that can easily integrate with your ERP, WMS, or other critical systems?
A seamless integration will enable efficient data exchange and eliminate the need for manual data entry, reducing the risk of errors and delays.
- 2. Collaborate with internal and external stakeholders
Involve key stakeholders in the integration process, including IT, operations, finance, and external partners such as suppliers and logistics providers. Understand their requirements and ensure that the integration solution meets their needs. Collaborative integration efforts can streamline processes, improve data accuracy, and enhance overall supply chain visibility.
- 3. Test and validate the integration
Before going live, thoroughly test the integration between the supply chain visibility tool and other systems. Validate data accuracy, data flow, and system functionality. Conduct end-to-end testing across different scenarios to ensure that all critical processes are functioning as expected.
- 4. Monitor and continuously improve supply chain operations
Once the integration is complete, establish a monitoring mechanism to track the performance of the integrated systems. Regularly review the data and identify areas for improvement to enhance your supply chain management. Continuously seek feedback from users and stakeholders to identify any issues or bottlenecks that need to be addressed.
Measuring the Success of Supply Chain Visibility System
To determine the effectiveness of your supply chain visibility software, track and measure key performance indicators (KPIs) identified during the implementation phase. Regularly assess and report on these KPIs to monitor progress, identify areas for improvement, and make data-driven decisions. Here are some additional measures of success in supply chain management:
– Improved on-time delivery performance
– Reduced order fulfillment cycle times
– Increased inventory turnover and reduced carrying costs
– Enhanced collaboration and communication with suppliers and logistics providers
– Reduction in supply chain disruptions and unplanned events
– Improved customer satisfaction and loyalty
Conclusion
Implementing and integrating supply chain visibility software is a strategic move that can revolutionize your supply chain operations. By following the best practices outlined in this blog, you can ensure a successful implementation of the supply chain visibility tool. This will optimize your supply chain processes, and gain a competitive edge in the market. Remember that supply chain visibility is an ongoing journey, and continuous improvement is key to achieving sustainable success.
Are you ready to embrace the power of technology? Leverage the benefits of the supply chain visibility system, and transform your supply chain into a well-oiled machine. Click on the red button to talk with an expert to enhance your supply chain management.
128
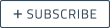
@LogiNext