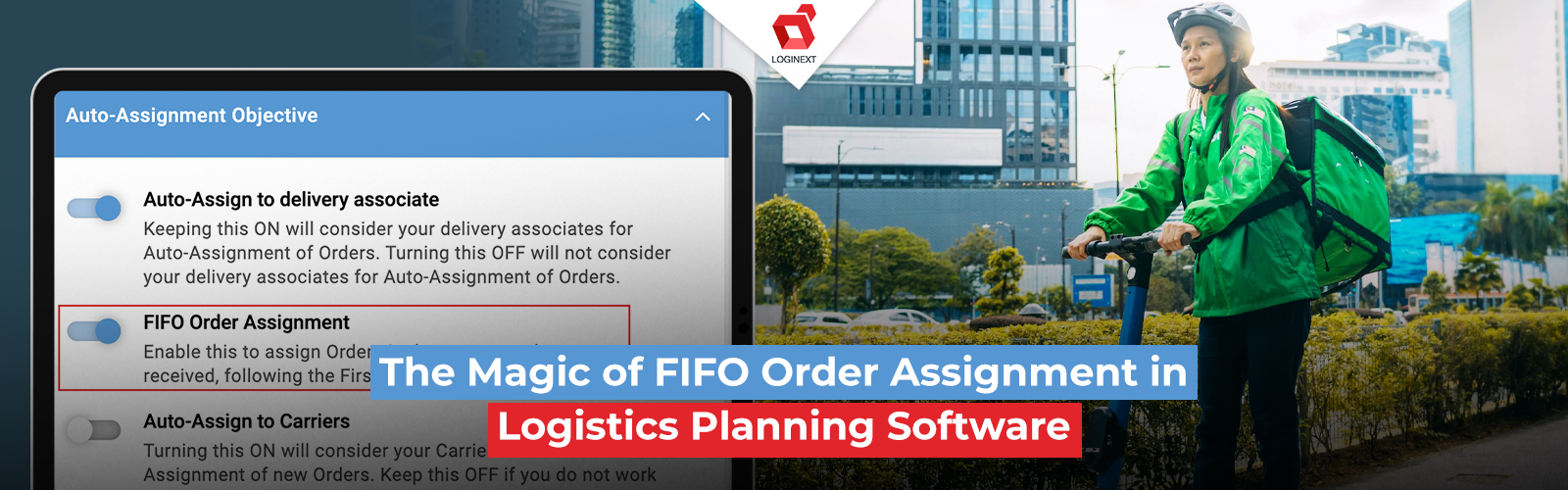
The Magic of FIFO Order Assignment in Logistics Planning Software
As the race of final mile delivery heats up, the concept of FIFO Order Assignment in Logistics Planning Software is making headlines. If you are one of those curious minds who have wondered how order prioritization takes place you’re in for a treat. Today, we will discuss in detail the heart of delivery optimization and how orders reach you promptly.
Understanding FIFO Order Assignment in Logistics Planning Software
Unlocking the Power for Delivery Associates:
If you’re managing delivery associates, enabling FIFO Order Assignment is your ticket to a more organized and streamlined workflow. This feature allows the Auto-assignment engine to prioritize orders based on the ‘First-In, First-Out’ principle.
Picture this: The engine creates queues of orders at each pickup location, standing in the sequence they were received. While the first in line gets first dibs on auto-assignment. The engine considers various parameters, like skill set matches, ensuring the best possible assignment for each order.
The Queue Dynamics:
FIFO Order Assignment works by creating queues at pickup locations, each order patiently waiting its turn. The logistics planning software engine endeavors to auto-assign the first order in the queue before moving on to the next. However, it’s a race against time, defined by the Maximum Queue Time parameter. The priority remains with the first order until its time in the queue expires.
Balancing Between Delivery Associates and Carriers:
But what if you’re managing both delivery associates and carriers? Fear not – FIFO Order Assignment has you covered. Beyond enabling it for delivery associates, you gain the power to specify your Auto-assignment Objective Preference. Choose whether you want delivery associates or carriers to take the lead in the auto-assignment of new orders, adding an extra layer of customization to your logistics planning software.
Behind the Scenes of an Auto-assignment Engine’s Strategy
While FIFO Order Assignment is a beacon of efficiency, the engine considers more than just order sequence. Skill set matches, delivery associate availability, and the unique Auto-assignment Objective Preference all play a role in order assignment in logistics planning software. Once the FIFO Order Assignment configuration is turned ON, set the maximum queue time for delivery associates and carriers. Set the preference for which fleet is to be prioritized for carrying out the orders. Set the order preparation time (in minutes) before the auto-assignment starts.
Enhancing Efficiency With FIFO Order Assignment in Logistics Planning Software
In a world where time is of the essence, FIFO Order Assignment emerges as a strategic ally in the pursuit of streamlined logistics. It’s not just about assigning orders; it’s about streamlining deliveries that prioritize not just speed but also precision.
FIFO vs LIFO: Which side are you on when planning logistics operations?
FIFO (First-In, First-Out):
1. Principle:
– Order of Priority: The logistics planning software prioritizes the orders based on the sequence in which they were received.
– Queue Dynamics: Creates queues of orders at pickup locations, and the order at the front of the queue is considered for assignment first.
2. Operational Dynamics:
– Sequential Processing: Logistics planning software follows a sequential processing model, aiming to fulfill orders in the order they were received.
– Time Sensitivity: Assigns priority to orders based on their time in the queue, with a defined Maximum Queue Time parameter.
3. Advantages:
– Fairness: The logistics planning software ensures a fair and transparent order assignment process based on the order creation sequence.
– Consistency: Offers predictability as orders are processed in a structured, first-come-first-served manner.
4. Considerations:
– Time Constraints: Ideal for scenarios where there are time-sensitive deliveries and maintaining the order sequence is crucial.
LIFO (Last-In, First-Out):
1. Principle:
– Order of Priority: Here the logistics planning software prioritizes the most recently received orders over earlier ones.
– Dynamic Assignment: Doesn’t adhere strictly to the order in which orders were received; recent orders take precedence.
2. Operational Dynamics:
– Flexibility: Allows for more flexibility in the assignment process, as the most recent orders are considered first.
– Varied Processing: Orders may not be processed sequentially, as the system prioritizes the most recent additions.
3. Advantages:
– Adaptability: Well-suited for scenarios where there is flexibility in processing orders and recent orders are of higher importance.
– Dynamic Prioritization: The logistics planning software enables adaptability to changing circumstances or urgent requirements.
4. Considerations:
– Dynamic Demands: Suitable for situations where the urgency of recent orders may override the chronological order.
How to Choose between FIFO and LIFO for your Logistics Planning Software?
FIFO | LIFO | |
Nature of Deliveries | Best suited for scenarios where maintaining the chronological order of order fulfillment is critical, such as perishable goods or time-sensitive deliveries. | Ideal for scenarios where the urgency of recent orders takes precedence, and adaptability in processing is crucial. |
Operational Constraints | Provides structure and predictability, suitable for operations where maintaining a strict order is a priority. | Offers flexibility, making it suitable for dynamic environments where priorities may shift. |
Customer Expectations | Aligns with customer expectations of orders being fulfilled in the order they were placed. | This may be preferable when meeting urgent customer demands is a higher priority. |
In summary, the choice between FIFO and LIFO in logistics planning software depends on the specific needs, constraints, and priorities of the logistics operation. Both strategies have their merits, and the decision should align with the unique dynamics of the business and its delivery objectives.
Real-world Examples Where FIFO in Logistics Planning Software is Useful to Businesses
Let’s consider a real-world example in the context of a perishable goods supply chain, such as the food industry. In this scenario, the use of FIFO (First-In, First-Out) in inventory management and order fulfillment is crucial for maintaining product quality and adhering to freshness standards.
Scenario: FIFO in Perishable Goods Supply Chain
Imagine a distribution center for a fresh produce supplier, dealing with items like fruits and vegetables. These goods have a limited shelf life, and their quality degrades over time. Maintaining freshness is not only a quality standard but also a regulatory requirement and a customer expectation.
Inventory Management:
Incoming Shipments: As new shipments of fresh produce arrive at the distribution center, each pallet or crate is assigned a timestamp indicating when it was received. This establishes the chronological order of the inventory.
Storage: The goods are stored in the warehouse with the oldest items at the front, ensuring that the items closest to their expiration date are easily accessible.
Order Fulfillment:
Picking and Packing: When customer orders come in, the FIFO system dictates that the items with the earliest expiration dates are selected first for order fulfillment. This ensures that the oldest inventory is used before newer arrivals.
Shipping: The picked items are then packed and dispatched, maintaining the order in which they were received. This aligns with the FIFO principle, where the first items to enter the inventory are the first to be sent out.
Benefits of FIFO in the Perishable Goods Supply Chain
Quality Assurance: FIFO helps ensure that the freshest items are sent to customers, reducing the risk of selling or shipping items close to their expiration date.
Regulatory Compliance: In industries where adherence to regulations is paramount, FIFO supports compliance by managing inventory in a way that aligns with industry standards.
Customer Satisfaction: Meeting or exceeding customer expectations for freshness leads to higher satisfaction and loyalty.
Benefits of FIFO in the F&B Industry
Freshness Assurance: FIFO ensures that the ingredients used in customer orders are as fresh as possible, contributing to the overall quality and taste of the food.
Inventory Management: By systematically using the oldest ingredients first, the restaurant minimizes the risk of items expiring or losing quality before being utilized.
Reduced Waste: FIFO helps reduce food waste by preventing ingredients from sitting in inventory for too long, leading to a more efficient use of resources.
Consistency: FIFO contributes to the consistency of the food, ensuring that customers receive items with consistent quality and taste.
Efficient Service: By following FIFO, the kitchen staff can work more efficiently, reducing wait times for customers and contributing to a positive dining experience.
So, that’s a wrap from our end on the exploration of FIFO Order Assignment. They have become a must-have in logistics planning software. They help dispatchers not only with inventory management but seamless deliveries for maximum customer satisfaction. Feel free to learn more about how LogiNext helps implement FIFO for its customers in its logistics planning software. Click on the red button below and schedule an appointment.
92
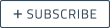
@LogiNext