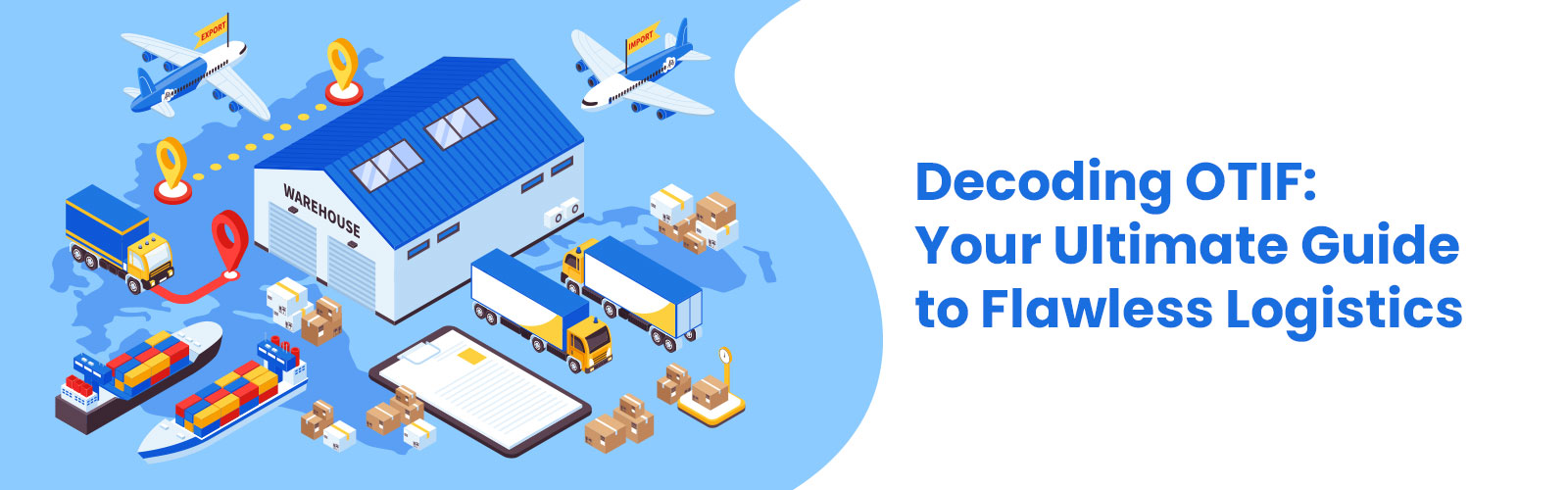
Decoding OTIF: Your Ultimate Guide to Flawless Logistics
In the fast-paced world of logistics and supply chain, the pressure to deliver more, faster, and with zero errors has never been higher. Customers no longer just expect timely deliveries—they demand them, along with complete and accurate orders. This is where On Time In Full (OTIF) steps in as a critical performance metric.
On Time In Full isn’t just another supply chain acronym. It’s a direct measure of how well a company fulfills its promises. It tells you whether a delivery arrived when it was supposed to—and with everything the customer ordered. In short, it’s a litmus test for supply chain reliability.
In this comprehensive guide, we’ll decode what OTIF means, why it matters, what affects it, and how the right solutions can drive higher performance and customer satisfaction.
What is On Time In Full?
On Time In Full (OTIF) is a performance indicator used to measure supply chain efficiency. It evaluates whether deliveries are made on the scheduled date (on-time) and with the correct quantity and items (in-full).
The On Time In Full Formula:
OTIF %=(Number of deliveries on time and in full/Total number of deliveries) * 100
For example, if you had 950 compliant deliveries out of 1,000, your OTIF score would be 95%.
Why OTIF Matters
A low score often translates to lost revenue, dissatisfied customers, and broken trust in the supply chain. Here’s why businesses can’t afford to ignore it:
1. Customer Satisfaction:
87% of customers say timely and complete deliveries impact their loyalty. On Time In Full directly influences repeat purchases and brand perception.
2. Operational Efficiency:
Poor scores usually point to deeper issues like inventory inaccuracies, transportation delays, or process bottlenecks. It acts as a mirror for internal performance.
3. Financial Performance:
In industries like retail or pharmaceuticals, low OTIF can lead to penalties, chargebacks, or lost contracts—directly affecting the bottom line.
Common Causes of Low OTIF Scores
Understanding the root causes of failures helps businesses fix systemic inefficiencies. Key factors include:
1. Inventory Mismatches:
Inaccurate stock levels, stockouts, or incorrect substitutions can result in incomplete or delayed orders, impacting the ‘in-full’ component of OTIF.
2. Poor Demand Forecasting:
When forecasts are off, businesses either understock or overstock, disrupting fulfillment schedules and leading to missed delivery windows.
3. Transportation Delays:
Inefficient routing, last-mile issues, or unforeseen disruptions like traffic or weather can derail on-time performance.
4. Order Processing Errors:
Mistakes in picking, packing, labeling, or documentation can lead to incorrect deliveries, reducing overall OTIF accuracy.
Strategies to Improve Performance
Improving On time in full is a multi-faceted effort. Here are proven ways businesses can enhance their delivery performance:
1. Implement the Best OTIF Software:
Using the best software allows companies to track delivery metrics in real time, identify trends, and automate alerts for delays or errors. These platforms integrate with existing WMS and TMS systems to offer end-to-end visibility. Advanced analytics help pinpoint recurring issues and improve planning accuracy.
2. Optimize Demand Forecasting:
Accurate forecasting helps prevent stockouts and overstocking, both of which negatively affect OTIF. AI-driven forecasting tools analyze historical sales, seasonality, and external factors like market trends to create more accurate demand plans. This ensures inventory availability aligns with customer orders.
3. Using Technology for Real-Time Visibility:
Technology such as IoT sensors, GPS tracking, and cloud-based platforms provide real-time insights across the supply chain. Businesses can monitor vehicle locations, shipment conditions, and warehouse activity, reducing unexpected disruptions and improving overall responsiveness.
4. Streamline Order Fulfillment Process:
Automation in picking, packing, and labeling minimizes human errors and speeds up operations. Barcode scanning and RFID systems ensure order accuracy, while robotic systems can boost throughput. A streamlined fulfillment process guarantees that products are shipped quickly and correctly, improving both timeliness and completeness.
Role of OTIF Solutions in Modern Logistics
Modern OTIF solutions go beyond dashboards and reports. They now leverage cutting-edge technologies like AI, machine learning, and predictive analytics to optimize every aspect of the supply chain. Here’s how:
1. Predictive Delivery Times:
AI-powered systems analyze real-time traffic, weather data, and historical trends to forecast accurate delivery windows, reducing late arrivals.
2. Automated Compliance Tracking:
OTIF solutions automatically monitor contracts and Service Level Agreements (SLAs), ensuring adherence to agreed-upon delivery times and conditions.
3. Anomaly Detection:
Machine learning algorithms can spot irregularities and potential delays before they occur, allowing for proactive intervention.
By incorporating these advanced capabilities, businesses that adopt these OTIF solutions experience up to a 20% improvement in their OTIF scores within just six months, enhancing overall operational efficiency and customer satisfaction.
Case Study: OTIF Improvement in Action
A global FMCG brand integrated a leading OTIF solution across its supply chain, transforming its operations. By leveraging AI-powered forecasting, live delivery tracking, and real-time inventory synchronization, the company was able to address inefficiencies and enhance delivery accuracy.
Within just three months, the OTIF score improved significantly from 88% to 97%. This boost in performance resulted in a 30% reduction in customer complaints due to fewer delays and errors.
Additionally, transportation efficiency saw a 15% improvement, as optimized routes and predictive analytics helped minimize disruptions. This case highlights the profound impact of OTIF solutions on overall logistics performance.
Future of OTIF: Smart, Predictive, and Autonomous
With the rise of AI, machine learning, and autonomous logistics, the future of OTIF is evolving from reactive to predictive. OTIF metrics will increasingly rely on AI to analyze vast amounts of real-time data, predicting potential delays, stockouts, or inventory mismatches before they occur. These systems will not only forecast failures but also recommend corrective actions in real time, allowing businesses to address issues proactively.
As autonomous logistics technologies, like self-driving trucks and drones, become mainstream, OTIF performance will be further optimized. The future of OTIF isn’t just about measuring performance—it’s about transforming the entire supply chain into a smarter, more efficient system.
Final Thoughts
On Time In Full (OTIF) is more than just a metric; it’s a reflection of operational excellence. In a world where customer satisfaction and brand loyalty hinge on reliable delivery, investing in the best software, using advanced solutions, and integrating cutting-edge technology can make all the difference.
Improving OTIF is not just a logistics initiative—it’s a business imperative. Discover how LogiNext’s advanced software can help you deliver on time, every time. From real-time visibility to AI-powered analytics, we’ve got the tools to elevate your logistics game. Click on the red button to book a demo today!
2
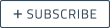
@LogiNext