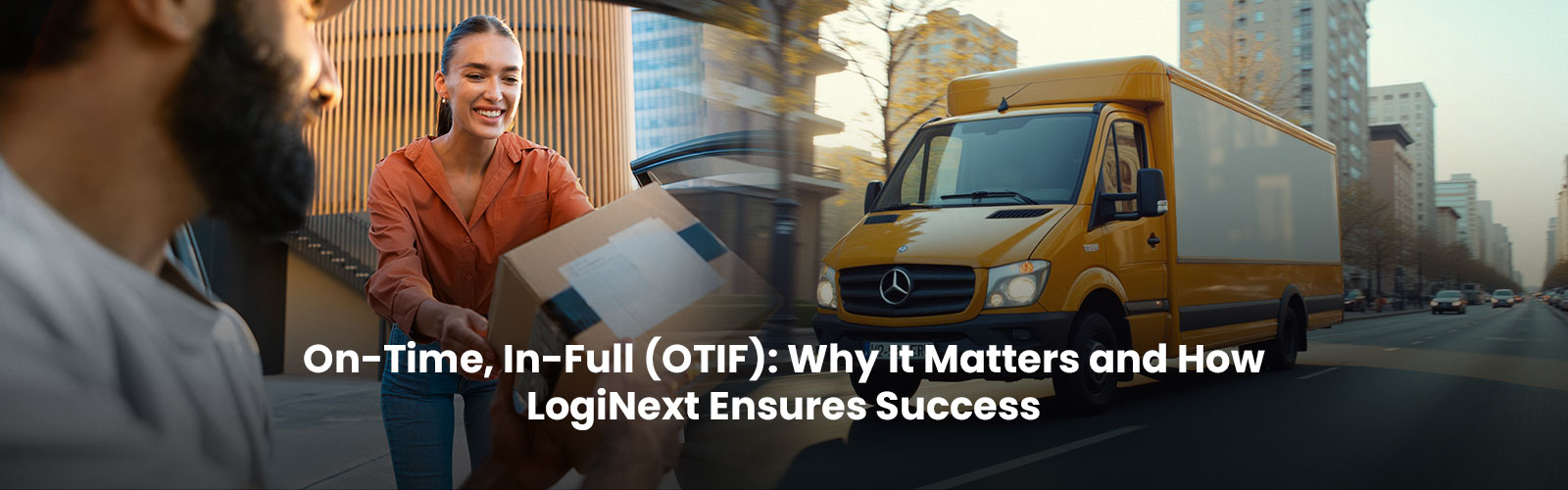
On-Time, In-Full (OTIF): Why It Matters and How LogiNext Ensures Success
In today’s fast-paced business environment, logistics plays a crucial role in customer satisfaction and overall success. One metric stands out as a key indicator of logistical excellence: On-Time, In-Full (OTIF). This blog post will delve into what is OTIF and why is it important in logistics. Exploring its significance and showcasing how LogiNext empowers businesses to achieve and exceed their OTIF targets.
Understanding On-Time, In-Full (OTIF)
OTIF represents the percentage of orders that are delivered to the customer on the agreed-upon delivery date and with all the correct items and quantities. It’s a comprehensive measure that goes beyond simply delivering on time. It emphasizes the completeness and accuracy of the order as well. A shipment is considered OTIF only if both the “on-time” and “in-full” criteria are met. Failing either one results in a missed OTIF target.
Why is OTIF so Important?
What is OTIF and why is it important in logistics? The answer is multifaceted. OTIF directly impacts several critical aspects of a business:
1. Customer Satisfaction:
Meeting delivery promises and providing the correct order builds trust and fosters strong customer relationships. Conversely, late or incomplete deliveries can lead to frustration, lost sales, and damage to brand reputation. In a world of instant gratification, customers expect timely and accurate deliveries. A study by Invespcro found that 93% of customers are more likely to be loyal to a company after a positive delivery experience.
2. Cost Reduction:
Inefficient logistics and missed OTIF targets can result in increased costs. These costs can stem from expedited shipping, return processing, customer service inquiries, and even lost revenue due to dissatisfied customers. Optimizing for OTIF helps minimize these expenses. A report by McKinsey suggests that supply chain disruptions can cost companies millions of dollars annually, with some estimates reaching as high as 5% of revenue.
3. Improved Operational Efficiency:
Achieving high OTIF rates requires streamlined logistics processes. This includes efficient warehouse management, optimized routing, real-time tracking, and proactive communication. Focusing on OTIF drives improvements across the entire supply chain.
4. Competitive Advantage:
In a competitive market, businesses that consistently achieve high OTIF scores differentiate themselves. They become the preferred choice for customers seeking reliable and dependable service. This can translate into increased market share and profitability.
5. Data-Driven Insights:
Tracking and analyzing OTIF performance provides valuable insights into logistics operations. This data can be used to identify bottlenecks, optimize processes, and make informed decisions to further improve OTIF rates.
How to Improve OTIF Performance
How to improve OTIF performance in supply chain management? This is a question many businesses grapple with. Fortunately, several strategies can be implemented to boost OTIF rates:
1. Optimize Delivery Routes:
Efficient route planning is essential for on-time delivery. Utilizing route optimization software can help minimize travel time, reduce fuel consumption, and ensure that deliveries are made within the designated time windows.
2. Real-Time Tracking and Visibility:
Having real-time visibility into the location and status of shipments is crucial. This allows businesses to proactively address potential delays and keep customers informed. GPS tracking and telematics provide valuable insights into the movement of goods.
3. Inventory Management:
Maintaining optimal inventory levels is vital for fulfilling orders in full. Accurate demand forecasting and efficient warehouse management systems help prevent stockouts. This helps to ensure that the necessary items are available when needed. A study by Aberdeen Group found that best-in-class companies have inventory accuracy levels above 95%. While average companies struggle with accuracy closer to 80%.
4. Proactive Communication:
Keeping customers informed about the status of their orders is essential. Proactive communication helps manage expectations and reduces the likelihood of complaints. Automated notifications and tracking updates can be used to keep customers in the loop.
5. Collaboration with Suppliers and Carriers:
Strong relationships with suppliers and carriers are crucial for ensuring timely and complete deliveries. Open communication and collaboration can help address potential issues and improve overall supply chain performance.
Best Strategies to Achieve On-Time, In-Full (OTIF) Delivery
Best strategies to achieve On-Time, In-Full (OTIF) delivery often involve leveraging technology. LogiNext offers a comprehensive suite of solutions designed to help businesses optimize their logistics operations and achieve their OTIF goals.
1. Advanced Route Planning and Optimization:
LogiNext’s route optimization software considers various factors, such as traffic conditions, delivery windows, and vehicle capacity, to create the most efficient routes. This helps minimize travel time and ensures on-time delivery.
2. Real-Time Tracking and Visibility:
LogiNext provides real-time visibility into the location and status of shipments. This allows businesses to monitor deliveries, identify potential delays, and proactively address any issues.
3. Order Management and Fulfillment:
LogiNext’s order management system streamlines the order fulfillment process, from order placement to delivery. This helps ensure that orders are processed accurately and efficiently.
4. Delivery Management and Proof of Delivery:
LogiNext’s delivery management tools enable businesses to manage deliveries effectively and capture electronic proof of delivery. This helps reduce disputes and ensures that deliveries are completed accurately.
5. Analytics and Reporting:
LogiNext provides detailed analytics and reporting on OTIF performance. This data can be used to identify areas for improvement and make informed decisions to further optimize logistics operations.
How to Measure and Track OTIF in Logistics Operations
The formula for calculating OTIF is simple:
OTIF (%) = (Number of OTIF Orders / Total Number of Orders) * 100
However, effectively tracking OTIF requires more than just a formula. Businesses need to implement systems that capture data on delivery times, order accuracy, and other relevant metrics. LogiNext’s platform provides the tools and dashboards necessary to monitor and analyze OTIF performance in real time.
Also Read: 5 Best Logistics Management Software for E-Commerce
Conclusion
On-Time, In-Full (OTIF) delivery is a key metric for businesses aiming to enhance customer satisfaction and reduce costs. It also helps companies gain a competitive advantage by ensuring reliable and efficient order fulfillment. By implementing the right strategies, businesses can optimize their logistics operations and improve efficiency. Leveraging technology like LogiNext’s platform further helps them achieve their OTIF targets. Focusing on OTIF is not just about meeting a metric; it’s about building trust, fostering customer loyalty, and driving sustainable growth. So, click on the red button below and book a demo with LogiNext. Take the plunge and change your business forever.
39
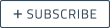
@LogiNext