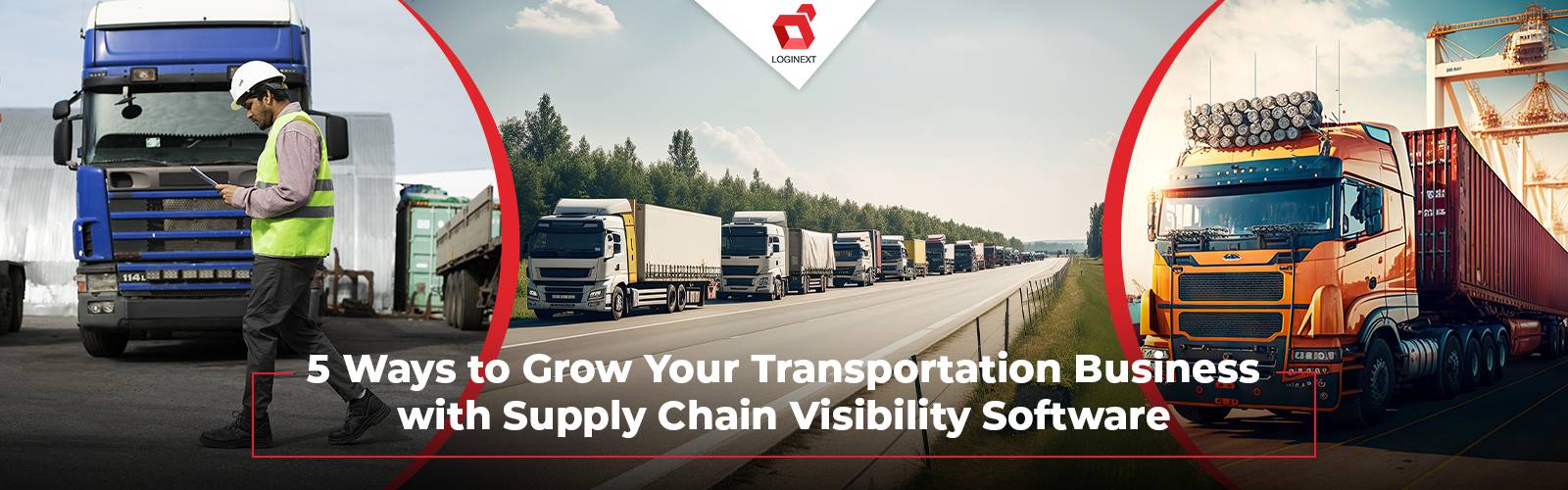
From Zero Visibility to End-to-End Control: 5 Ways to Grow Your Transportation Business with Supply Chain Visibility Software
Did you know that 69% of transportation businesses cite lack of visibility as their primary obstacle to achieving operational efficiency? This statistic reveals a critical challenge in an industry where timely deliveries and precise coordination are crucial. Imagine running a business where you cannot track your shipments in real-time, predict delays, or optimize routes effectively. The ripple effects of such limitations are vast, impacting everything from customer satisfaction to overall profitability. Here, supply chain visibility software become crucial to meet modern logistics and supply chain demands.
In today’s fast-paced and highly competitive transportation industry, visibility is no longer a luxury—it’s a necessity. However, many companies struggle with outdated systems and processes that provide little to no visibility into their supply chains. This lack of transparency can lead to issues like unexpected delays, increased operational costs, and poor customer service. Without the ability to monitor and manage every aspect of the supply chain, businesses are often left reacting to problems rather than proactively preventing them. This reactive approach not only hampers growth but also significantly affects the bottom line.
Today we address these pressing issues by exploring how supply chain visibility software can revolutionize your transportation business. This technology empowers businesses to move from zero visibility to end-to-end control by providing real-time insights, enhanced analytics, and seamless collaboration. We will delve into five ways an ideal supply chain visibility software can help you streamline operations, reduce costs, and ultimately drive growth. Whether you’re looking to enhance customer satisfaction or achieve greater operational efficiency, get the insights and solutions you need to transform your business.
Real-Time Tracking and Monitoring With Supply Chain Visibility Software
Current Challenge
In the transportation industry, real-time tracking and monitoring are crucial for maintaining efficiency and meeting customer expectations. Without these capabilities, companies face significant challenges:
Delays: One of the most common issues is the inability to anticipate and manage delays. Without real-time tracking, it’s difficult to pinpoint the exact location of a shipment, leading to uncertainty and disruptions in the supply chain.
Lost Shipments: Shipments can go missing due to poor tracking systems, causing significant financial losses and eroding customer trust.
Inefficient Resource Utilization: Without accurate data, resources such as drivers, vehicles, and fuel are not optimally used, leading to increased operational costs.
Poor Customer Service: Customers today expect timely updates and precise delivery times. Lack of real-time information leads to poor communication and dissatisfaction.
Reactive Problem Solving: Businesses often find themselves in a constant state of reaction, trying to manage crises instead of preventing them.
These issues not only disrupt operations but also have a cascading effect on overall business performance, leading to increased costs and diminished customer trust.
Solution
Supply chain visibility software addresses these challenges by providing real-time data on shipments. This technology integrates with various tracking devices and systems, offering a comprehensive view of the supply chain:
GPS Tracking: Provides live updates on the exact location of shipments, allowing businesses to monitor progress in real-time.
Status Updates: Real-time alerts on the status of shipments, including departure and arrival times, delays, and any deviations from planned routes.
Predictive Analytics: Uses historical and real-time data to predict potential delays and suggest alternative routes.
Centralized Dashboard: Offers a unified view of the entire supply chain, making it easier to manage and coordinate shipments.
By implementing these features, businesses can transition from reactive to proactive management, ensuring smoother and more efficient operations.
Benefits
Reduced Delays: With real-time data, companies can anticipate and mitigate delays by rerouting shipments or adjusting schedules proactively.
Improved Customer Satisfaction: Accurate and timely updates enhance customer communication and trust, leading to higher satisfaction and loyalty.
Proactive Issue Resolution: Early detection of potential problems allows for quick resolution, preventing minor issues from escalating into major disruptions.
Optimized Resource Utilization: Real-time data helps in better planning and utilization of resources, reducing operational costs and improving efficiency.
Enhanced Transparency: A transparent supply chain fosters better relationships with partners and customers, as everyone has access to accurate and up-to-date information.
Read More: 5 Ways Live Screen Helps Enhance Real-Time Visibility Platform
Case Study: How FedEx Handles Real-Time Tracking and Monitoring Issues Using Supply Chain Visibility Software?
FedEx, a global leader in transportation and logistics, faced significant challenges in managing its vast network of shipments across the globe. Delays and lost packages were common issues, negatively impacting customer satisfaction and operational efficiency. To address these challenges, FedEx implemented advanced supply chain visibility software.
Implementation of GPS Tracking: FedEx equipped its vehicles and containers with GPS tracking devices. This allowed the company to monitor the exact location of every shipment in real-time.
Real-Time Alerts: The software provided instant alerts on any delays or route deviations, enabling quick decision-making to reroute shipments and avoid further delays.
Centralized Control Center: FedEx established a centralized control center that utilized the visibility software to monitor all shipments globally. This control center could intervene in real-time to resolve issues as they arose.
Results:
Reduced Delays: The real-time tracking capability reduced delays by 30%, as FedEx could proactively manage potential disruptions.
Increased Customer Satisfaction: Customers received timely updates about their shipments, improving their overall experience and trust in FedEx services.
Operational Efficiency: FedEx optimized its resource utilization, reducing fuel costs and improving the efficiency of its delivery network.
Revenue Growth: With improved operations and customer satisfaction, FedEx saw a notable increase in revenue, reinforcing the value of their investment in visibility software.
By adopting supply chain visibility software, FedEx transformed its operations, setting a benchmark in the industry for real-time tracking and monitoring. This case illustrates how such technology can substantially improve efficiency, customer satisfaction, and overall business performance.
Enhanced Data Analytics and Reporting Using Supply Chain Visibility Software
Current Challenge
In the transportation industry, traditional methods of data collection and reporting often fall short, leading to several inefficiencies:
Fragmented Data: Data is usually scattered across multiple systems and formats, making it difficult to consolidate and analyze.
Lack of Real-Time Insights: Traditional reporting methods often rely on historical data and manual input, which delay insights and limit the ability to make timely decisions.
Inaccurate Forecasting: Without detailed analytics, predicting future trends and demands is challenging, leading to overstocking or stockouts.
Limited Visibility: Managers and stakeholders lack a holistic view of the supply chain, making it hard to identify bottlenecks and inefficiencies.
Reactive Management: Decision-making is typically reactive rather than proactive, addressing issues after they occur rather than preventing them.
These inefficiencies can result in increased costs, missed opportunities, and reduced competitiveness in the market.
Solution
Supply chain visibility software transforms data collection and reporting by aggregating data from various sources and generating comprehensive, actionable reports. Here’s how it works:
Data Aggregation: The software integrates with various systems (e.g., GPS tracking, ERP, WMS) to collect data in real-time, providing a unified view of the supply chain.
Advanced Analytics: Uses sophisticated algorithms to analyze data, uncover patterns, and generate insights.
Customizable Dashboards: Offers customizable dashboards that present key metrics and KPIs in an easy-to-understand format.
Automated Reporting: Automates the generation of detailed reports on various aspects of the supply chain, such as performance, inventory levels, and delivery times.
Predictive Analytics: Utilizes historical data and machine learning to predict future trends and potential issues, enabling proactive management.
Benefits
Data-Driven Decision Making: With comprehensive and accurate data, businesses can make informed decisions, improving efficiency and effectiveness.
Trend Analysis: Identify and analyze trends over time, helping to understand market dynamics and adjust strategies accordingly.
Predictive Analytics: Anticipate future demand and supply chain disruptions, allowing for proactive measures to be taken.
Improved Forecasting: Enhanced forecasting accuracy helps in better inventory management, reducing the risk of overstocking or stockouts.
Operational Efficiency: Detailed insights into every aspect of the supply chain help in identifying and eliminating inefficiencies, leading to cost savings.
Strategic Planning: Businesses can develop more effective strategies based on comprehensive data analysis and reporting.
Deep Dive: Enhancing Logistics And Supply Chain Efficiency With Generative AI In Reports And Analytics
Case Study: How Did Walmart Integrate Enhanced Data Analytics and Reporting Using Supply Chain Visibility Software?
Walmart, one of the world’s largest retail corporations, faced significant challenges in managing its vast and complex supply chain. The traditional methods of data collection and reporting were insufficient to handle the scale and speed required to maintain optimal inventory levels and ensure timely deliveries.
Implementation of Supply Chain Visibility Software:
Data Aggregation: Walmart implemented an advanced supply chain visibility software that aggregated data from its ERP systems, warehouse management systems, and transportation management systems.
Advanced Analytics: The software used machine learning algorithms to analyze historical data and provide real-time insights into inventory levels, demand patterns, and supply chain performance.
Customizable Dashboards: Walmart’s managers and stakeholders were provided with customizable dashboards displaying critical KPIs, enabling them to monitor performance and make informed decisions.
Automated Reporting: The software automated the generation of detailed reports, providing insights into various aspects of the supply chain, including vendor performance, inventory turnover, and delivery times.
Predictive Analytics: Utilizing predictive analytics, Walmart could forecast demand more accurately, adjust inventory levels, and anticipate potential supply chain disruptions.
Results:
Improved Forecasting: Walmart achieved a 25% improvement in forecasting accuracy, reducing the risk of overstocking and stockouts.
Enhanced Inventory Management: With better visibility and insights, Walmart optimized its inventory levels, resulting in a 15% reduction in inventory carrying costs.
Operational Efficiency: The insights from detailed analytics enabled Walmart to streamline its supply chain operations, reducing operational costs by 20%.
Increased Customer Satisfaction: Timely and accurate deliveries improved customer satisfaction and loyalty, contributing to increased sales and revenue.
Proactive Management: Predictive analytics allowed Walmart to anticipate and mitigate potential disruptions, ensuring a smoother and more reliable supply chain.
By leveraging enhanced data analytics and reporting through supply chain visibility software, Walmart transformed its supply chain management, achieving significant improvements in efficiency, cost savings, and customer satisfaction. This case highlights the transformative potential of advanced analytics in the transportation and logistics industry.
Improved Collaboration Across the Supply Chain Using Supply Chain Visibility Software
Current Challenge
In the transportation industry, poor communication and operational silos pose significant challenges. These issues can severely impact the efficiency and effectiveness of the supply chain:
Operational Silos: Different departments and partners often operate in isolation, using disparate systems that do not communicate with each other. This leads to fragmented processes and a lack of coordinated efforts.
Poor Communication: Inefficient communication channels between suppliers, carriers, and customers result in misunderstandings, delays, and errors. Important information often gets lost or delayed.
Inconsistent Data: Data is not shared consistently across the supply chain, leading to discrepancies and a lack of a single source of truth. This hampers decision-making and can cause conflicts between stakeholders.
Delayed Responses: Without real-time information sharing, responses to issues are delayed. This reactive approach often exacerbates problems rather than resolving them efficiently.
Reduced Accountability: When there is no clear communication or shared data, it becomes difficult to hold parties accountable for their roles in the supply chain, leading to finger-pointing and unresolved issues.
These challenges result in inefficiencies, increased costs, and decreased customer satisfaction, highlighting the critical need for improved collaboration across the supply chain.
Solution
Supply chain visibility software plays a pivotal role in enhancing collaboration among suppliers, carriers, and customers by providing a unified platform for data sharing and communication:
Unified Data Platform: The software integrates various systems and data sources, providing a single, centralized platform where all stakeholders can access the same information in real-time.
Real-Time Communication: Facilitates real-time communication and updates, ensuring that all parties are informed about the current status of shipments and any issues that arise.
Collaborative Tools: Offers tools such as shared dashboards, collaborative workspaces, and instant messaging, enabling seamless interaction and coordination between different parties.
Automated Notifications: Sends automated alerts and notifications to relevant stakeholders about critical events, such as delays or route changes, ensuring timely responses.
Role-Based Access: Provides role-based access to information, ensuring that each stakeholder can access relevant data without compromising security or privacy.
By leveraging these features, businesses can break down silos, improve communication, and enhance collaboration across the entire supply chain.
Benefits
Synchronized Operations: With all stakeholders accessing the same real-time information, operations become more synchronized, leading to smoother and more efficient workflows.
Shared Data Platforms: A shared data platform ensures consistency and accuracy of information, reducing discrepancies and enhancing trust among partners.
Enhanced Partnerships: Improved communication and transparency foster stronger relationships and partnerships, as all parties are aligned and working towards common goals.
Proactive Issue Resolution: Real-time communication and collaborative tools enable quick identification and resolution of issues, preventing minor problems from escalating.
Increased Accountability: Clear visibility and communication make it easier to hold parties accountable, leading to better performance and reliability.
Cost Savings: Enhanced collaboration reduces inefficiencies and redundancies, leading to significant cost savings.
Discover: 10 Must-Have Integrations To Exponentially Grow Digital Commerce Businesses
Case Study: Learn How Procter & Gamble (P&G) Improved Collaboration Across the Supply Chain With Help of Supply Chain Visibility Software
Procter & Gamble, a global consumer goods company, faced significant challenges in managing its complex supply chain. The lack of collaboration among suppliers, carriers, and distributors led to frequent delays, increased costs, and reduced efficiency.
Implementation of Supply Chain Visibility Software:
Unified Platform: P&G implemented a supply chain visibility software that integrated data from all partners into a single, unified platform.
Real-Time Communication: The software facilitated real-time communication between suppliers, carriers, and P&G’s internal teams, ensuring everyone was informed about shipment statuses and any issues.
Collaborative Tools: Provided collaborative tools, such as shared dashboards and instant messaging, enabling seamless coordination and problem-solving among all stakeholders.
Automated Notifications: Set up automated notifications to alert relevant parties about critical events, such as delays or changes in delivery schedules.
Results:
Improved Coordination: The unified platform and real-time communication improved coordination among all parties, reducing delays and ensuring timely deliveries.
Enhanced Transparency: All stakeholders had access to the same real-time data, leading to greater transparency and trust. This transparency helped in better planning and execution of supply chain activities.
Proactive Problem-Solving: With collaborative tools and automated notifications, issues were identified and resolved proactively, preventing minor problems from escalating and causing major disruptions.
Cost Reduction: Improved collaboration and synchronization led to a 15% reduction in operational costs, as inefficiencies and redundancies were minimized.
Increased Efficiency: The streamlined processes and enhanced communication resulted in a 20% increase in overall supply chain efficiency.
Stronger Partnerships: The transparency and improved communication fostered stronger relationships with suppliers and carriers, leading to more reliable and resilient supply chain partnerships.
By adopting supply chain visibility software, Procter & Gamble significantly enhanced collaboration across its supply chain, achieving substantial improvements in efficiency, cost savings, and operational reliability. This case illustrates how improved collaboration, facilitated by advanced visibility tools, can transform supply chain management and drive business success.
Increased Operational Efficiency Using Supply Chain Visibility Software
Current Challenge
Operational efficiency is paramount in the transportation industry, where margins can be thin, and customer expectations are high. However, without proper visibility software, companies face several inefficiencies in resource allocation and process management:
Inefficient Route Planning: Without real-time data, planning optimal routes becomes challenging. This leads to longer travel times, increased fuel consumption, and higher operational costs.
Poor Schedule Management: Inadequate visibility into shipment statuses and delays results in suboptimal scheduling of deliveries and pickups. This causes missed deadlines and inefficient use of assets.
Underutilization of Resources: Lack of visibility into the status and location of assets (e.g., vehicles, drivers) leads to underutilization, with some resources being overused while others remain idle.
Increased Downtime: Unplanned downtimes and maintenance issues arise from a lack of predictive insights, leading to disrupted operations and additional costs.
Inconsistent Service Levels: Without a streamlined process, maintaining consistent service levels becomes difficult. This results in lower customer satisfaction and potential loss of business.
These challenges collectively contribute to higher operational costs, inefficient use of resources, and an inability to meet customer demands effectively.
Solution
Supply chain visibility software can significantly enhance operational efficiency by optimizing routes, schedules, and resource utilization through the following means:
Route Optimization: The software uses real-time traffic data, weather conditions, and historical delivery times to calculate the most efficient routes for each shipment, reducing travel time and fuel consumption.
Dynamic Scheduling: Integrates real-time shipment tracking and predictive analytics to adjust schedules dynamically, ensuring optimal use of vehicles and drivers.
Resource Utilization: Provides a comprehensive view of all assets. It enables better allocation of vehicles, drivers, and other resources based on real-time needs and availability.
Predictive Maintenance: Utilizes data analytics to predict maintenance needs and schedule timely interventions. Thus reducing unplanned downtimes and extending the lifespan of assets.
Centralized Dashboard: Offers a centralized dashboard that consolidates data from various sources. It allows for better monitoring, control, and coordination of operations.
Benefits
Cost Savings: By optimizing routes and schedules, companies can significantly reduce fuel consumption and operational costs. Efficient resource utilization also minimizes unnecessary expenses.
Reduced Fuel Consumption: Optimized routing and better vehicle management lead to lower fuel usage. It contributes to cost savings and a smaller environmental footprint.
Improved Service Levels: Consistent and reliable service levels enhance customer satisfaction and loyalty, potentially leading to increased business opportunities.
Increased Asset Utilization: Better visibility into asset status and availability ensures that resources are used efficiently, reducing idle time and maximizing productivity.
Proactive Maintenance: Predictive maintenance minimizes unplanned downtimes, ensuring smoother operations and reducing repair costs.
Enhanced Decision Making: Real-time data and analytics provide actionable insights, enabling more informed and strategic decision-making.
Read Now: Delivery Operations Optimization: Mastering Strategies For Efficiency And Driver Satisfaction
Case Study: How UPS Improves Operational Efficiency Using Supply Chain Visibility Software?
UPS, one of the world’s largest package delivery and supply chain management companies, faced significant challenges in managing its vast network of vehicles and deliveries efficiently. The company sought to improve its operational efficiency and reduce costs while maintaining high service levels.
Implementation of Supply Chain Visibility Software:
Route Optimization: UPS implemented an advanced supply chain visibility software that integrated real-time traffic data, weather conditions, and delivery schedules to optimize routes for its fleet.
Dynamic Scheduling: The software provided dynamic scheduling capabilities. It allows UPS to adjust delivery schedules in real-time based on changing conditions and shipment statuses.
Asset Management: UPS used the software to gain comprehensive visibility into its fleet of vehicles and drivers. It enabled better allocation and utilization of these resources.
Predictive Maintenance: The software’s predictive analytics capabilities helped UPS schedule proactive maintenance for its vehicles, reducing the risk of unplanned downtimes.
Centralized Control: A centralized dashboard provided UPS with a unified view of its operations, facilitating better monitoring and coordination.
Results:
Significant Cost Savings: Route optimization and dynamic scheduling led to a 10% reduction in fuel consumption. It also enables a notable decrease in overall operational costs.
Reduced Fuel Consumption: By optimizing routes, UPS saved millions of gallons of fuel annually. This contributes to cost savings and environmental sustainability.
Improved Service Levels: Enhanced scheduling and real-time visibility allowed UPS to meet delivery deadlines more consistently, improving customer satisfaction and loyalty.
Higher Asset Utilization: The comprehensive visibility into asset status enabled UPS to utilize its fleet more efficiently. It enables reduced idle time and maximized productivity.
Proactive Maintenance: Predictive maintenance reduced unplanned downtimes by 20%, ensuring smoother and more reliable operations.
Enhanced Decision Making: Real-time data and analytics provided UPS with valuable insights, enabling more strategic decision-making and operational improvements.
By leveraging supply chain visibility software, UPS achieved substantial improvements in operational efficiency, cost reduction, and service levels. This case highlights how advanced visibility tools can transform the transportation business, driving both efficiency and profitability.
Greater Customer Satisfaction and Loyalty With Supply Chain Visibility Software
Current Challenge
In the transportation industry, customer satisfaction and loyalty are crucial for sustained success. However, delayed or lost shipments can severely impact customer trust and satisfaction:
Delayed Shipments: When shipments are delayed, customers experience frustration and inconvenience, leading to dissatisfaction and potential loss of business.
Lost Shipments: Lost shipments cause significant disruptions, financial losses, and damage to a company’s reputation, eroding customer trust.
Lack of Transparency: Without real-time updates, customers remain uninformed about the status of their shipments, increasing anxiety and reducing trust.
Inconsistent Service: Irregular service levels make it difficult to build a reliable reputation. This leads to decreased customer loyalty and negative word-of-mouth.
Reactive Problem Solving: Companies without visibility software often react to problems after they occur, rather than preventing them, resulting in poor customer experiences.
These issues collectively damage the relationship between the transportation business and its customers. This emphasizes the need for reliable and transparent service.
Solution
End-to-end supply chain visibility software offers a robust solution to these challenges by ensuring transparency, reliability, and proactive management:
Real-Time Tracking: Provides customers with real-time updates on the status and location of their shipments, reducing anxiety and building trust.
Automated Notifications: Sends automated notifications to customers about key events. These include shipment departures, arrivals, and any delays, ensuring they are always informed.
Proactive Issue Management: Allows companies to identify potential issues before they impact customers and take proactive measures to resolve them.
Transparent Communication: Facilitates clear and consistent communication with customers, providing them with accurate information and setting realistic expectations.
Reliable Service: Enhances the company’s ability to deliver shipments on time and as promised, establishing a reputation for reliability.
Benefits
Building Trust: Consistent and transparent communication fosters trust, as customers feel informed and valued.
High Service Standards: Meeting delivery commitments and providing timely updates ensures high service standards, leading to satisfied customers.
Customer Loyalty: Satisfied customers are more likely to remain loyal and continue doing business with the company, contributing to sustained revenue.
Positive Reputation: Reliable and transparent service leads to positive word-of-mouth, attracting new customers and enhancing the company’s market position.
Proactive Problem Solving: By addressing potential issues before they affect customers, companies can maintain smooth operations and avoid negative experiences.
Recommended Read: How Last Mile Delivery Optimization Can Boost Customer Satisfaction
Case Study: Achieve Greater Customer Satisfaction and Loyalty Like DHL Using Supply Chain Visibility Software
DHL, a global leader in logistics and transportation, recognized the importance of customer satisfaction and sought to improve its service levels and reliability. The company faced challenges with delayed and lost shipments, impacting customer trust and satisfaction.
Implementation of Supply Chain Visibility Software:
Real-Time Tracking: DHL implemented visibility software that provided real-time tracking for all shipments, accessible by both DHL and its customers.
Automated Notifications: The software sends automated notifications to customers at key milestones. These include shipment dispatch, in-transit updates, and delivery confirmations.
Proactive Issue Management: DHL used the software to identify potential delays or disruptions early and took proactive measures to mitigate them.
Transparent Communication: The software enabled transparent communication with customers, providing accurate and timely updates about their shipments.
Reliable Service: By leveraging the visibility software, DHL improved its ability to meet delivery commitments consistently.
Results:
Increased Customer Trust: The real-time tracking and automated notifications significantly increased customer trust. This helps customers be always informed about their shipments.
Higher Satisfaction Ratings: DHL’s customer satisfaction ratings improved by 25%, as customers experienced fewer delays and appreciated transparent communication.
Enhanced Loyalty: The improvements in service and communication led to higher customer loyalty, with repeat business increasing by 20%.
Positive Reputation: DHL’s reputation for reliability and transparency grew, attracting new customers and strengthening its market position.
Proactive Problem Solving: The ability to address potential issues proactively reduced the number of complaints and negative experiences, further enhancing customer satisfaction.
By implementing supply chain visibility software, DHL significantly improved its customer satisfaction and loyalty. This demonstrates how transparency, proactive management, and reliable service can transform customer relationships and drive business success.
Transform Supply Chain Operations Using LogiNext’s Supply Chain Visibility Software
LogiNext’s supply chain visibility software provides comprehensive solutions for transportation businesses. It offers real-time tracking, giving you live updates on shipments. Enhanced analytics provide deep insights and data-driven decision-making. The software improves collaboration by unifying data and streamlining communication. Increased operational efficiency is achieved through optimized routes and resource utilization.
By implementing LogiNext, you can significantly reduce delays and operational costs. Real-time updates and transparency boost customer satisfaction and loyalty. Ultimately, LogiNext helps drive growth and success in your transportation business.
62
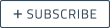
@LogiNext